A rocky ending is exactly what’s required
You can tell track construction on the southern section of the Narrabri to North Star Phase 1 project, between Narrabri and Bellata, is nearing completion when a ballast train arrives on site. Ballast distribution is one of the final stages of track construction and the arrival of the train marks a major milestone for the project.
August 29, 2022
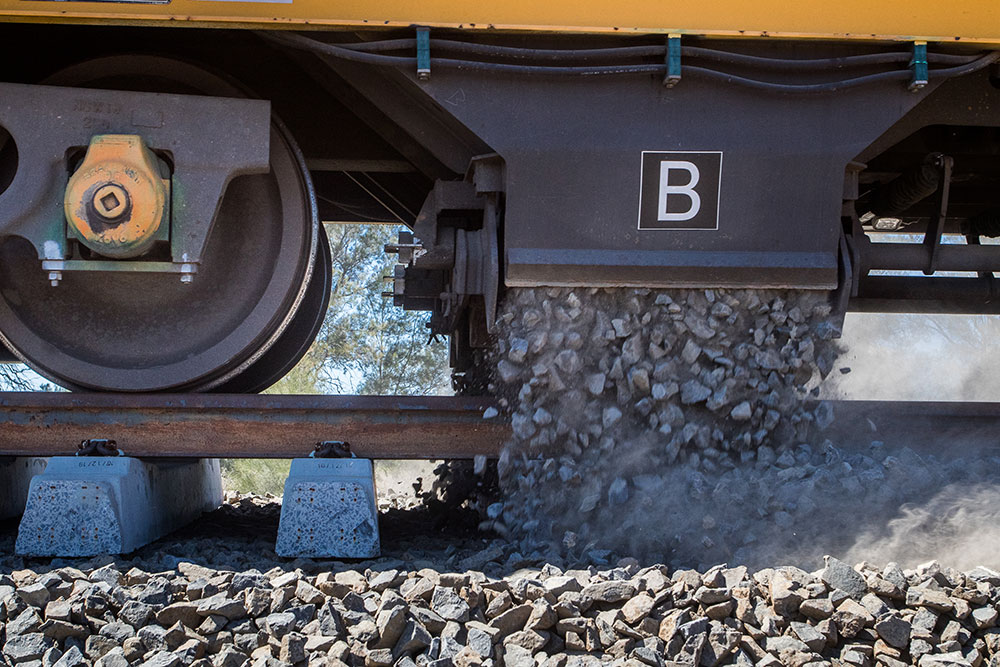
The train will be stationed near the University of Sydney Plant Breeding Institute, north of Narrabri until late August, after which it will head north dropping ballast in and around the new sleepers and tracks via doors at the bottom of each carriage.
Work on the southern section, which started in April 2022, is scheduled to finish at the end of October in time to enable freight trains to run during this year’s grain harvest season.
Ballast assists in stabilising the track bed, just like the ballast in a ship helps to keep it stable and upright. More than 365,000 tonnes of top and bottom ballast, made from basalt, have been delivered to sites along the Phase 1 project alignment, enough to fill 75 Olympic-size swimming pools!
Ballast also facilitates drainage around and beneath the track, so the ground’s cohesion is not compromised. The shape of the ballast is very important as each stone (ranging in size from 20mm to 63mm) must be irregular with sharp edges to ensure they properly interlock.
The ballast used on the Narrabri to North Star Phase 1 section is sourced locally through suppliers Johnstone Concrete and Quarries in Moree, Regional Group Australia and Mackellar Excavations.
Rail track is being laid in one of two ways on the Narrabri to North Star Phase 1 project – either as ‘skeleton’ track where the sleepers and track are laid directly onto the completed capping, or directly onto a completed mat of bottom ballast.
For a ‘skeleton’ track, the bottom ballast is dropped by the ballast train as it first passes over the skeleton track and is and then tamped and compacted into position under the sleepers as part of the subsequent track completion processes.
Where ‘skeleton’ track is not used, a 250mm layer of bottom ballast is first placed over the completed capping layer using a machine known as a paver. The sleepers and track are then placed directly on top of the paved bottom ballast layer.
In both situations, a final layer of ballast, known as the top ballast, is delivered and dropped by the ballast train as seen in the image above. The ballast trains on the project have up to 21 carriages, each with 55 tonnes of capacity.
The final step in the process is ballast quality control. First a ballast tamper, or tamping machine, compacts the ballast to make the tracks and track bed more durable and level, before a ground penetrating radar evaluates the condition of the ballast, ensuring it is at its optimal density.
IMAGES: (top) Close up of top ballast being dropped onto the train tracks from a carriage on a ballast train; (below) A paver machine laying down bottom ballast.